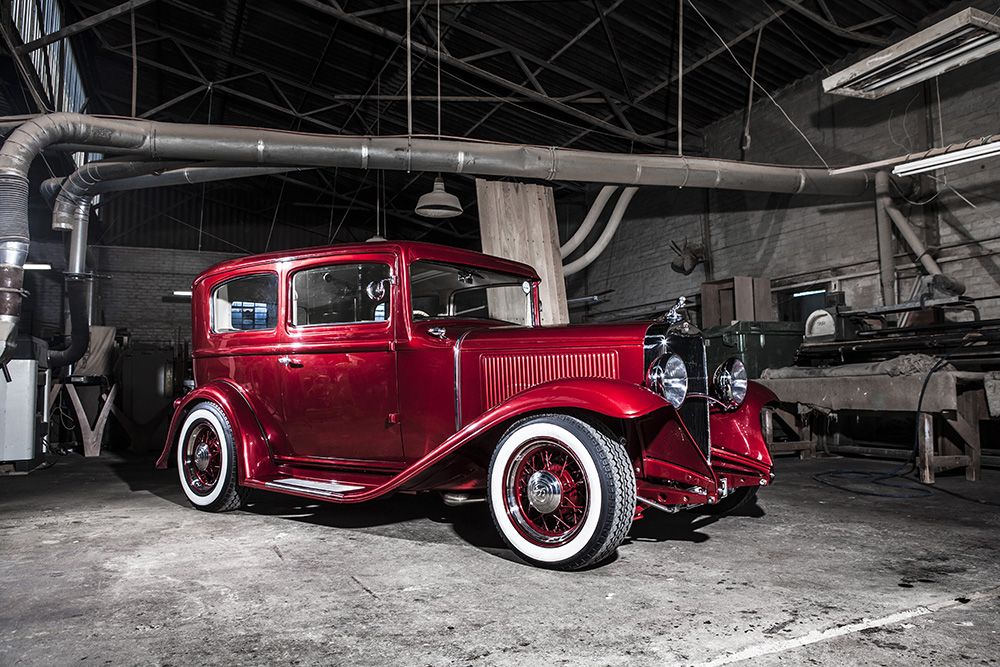
When Francois Carstens of Cape Select Furniture started looking for his ’48 Delivery (the one featured in our 2011 article), he placed an ad in a multitude of car magazines and newspapers all over the country. He was a year into the Delivery build when Andre Korff phoned him from Willowmore in the Eastern Cape.
Article by: Karl Eriksen
Photographs: Antigrafika
He told Francois that he has seen his ad in the paper and that he had a ’48 Ford van to sell. Francois was looking for a ’32 five-window coupe and Andre said that he did not have one of those but did have a 1931 Dodge Brothers. Francois did not know what it looked like and had pics sent to him. He and two friends made the trip out to Willowmore. But when he saw what condition it was in, he felt almost too embarrassed to tell his friends that perhaps they should just head home. So he loaded it up.
His approach was that this was the car’s last chance as the next step would have been taking it to a scrapyard. When people ask why he decided to tackle such a monumental task, his answer is that he just wanted to see if he could do it. He wanted to explore the different aspects of sheet metalwork and this would give him the freedom to express himself. Francois had previously completed a metalwork course with Barry Ashmole.
He made the entire nose, running boards, and one of the fenders. Then he changed it from the original four-door into a two-door. It came with the original chassis and almost the entire right-hand side of the body was rusted away. The chassis was repaired with patch panels, as were the fenders. He made patch panels by applying masking tape to the inside of the hole and then covering it with plaster of Paris or body filler.
The shape was then carved out perfectly and a fibreglass mould was made over that. The mould was then removed and then you have a thin 3mm fibreglass skin which is then turned upside down and placed into a purpose-made box. 1mm sheet metal is clamped around the sides and hamper-tapped by hand over a long period of time until you have the shape. It is then cut out and welded into place.
Francois made a rotisserie-like device for the body so that he could turn it himself. This was to avoid having to wake up his wife in the middle of the night for assistance. It originally had an open roof, covered with a combination of chicken mesh and sisal-like material, with a vinyl layer on top. For the radio, they ran a wire to the chicken mesh which acted like an aerial. But due to the fact that there is always a potential rust problem and issues with road-noise, he closed this up.
He made a wooden grate to get reference points in order to create the curve and shaped the metal over that. This probably gave him the biggest trouble, because it was such a large piece of metal which turned out perfectly until he welded it in place. When he welded one point, it would pull up at another. He had to cut it out and redo it. A 670 CFM Edelbrock carb feeds the 302 Ford V8 power plant, which is coupled to a BMW 5-series Getrag 5-speed box. Francois’s friend, Johan Theron, did all the mechanicals on the car. The suspension is from a Jaguar.
The Jag has 15-inch wheels and the Dodge has 17-inch wheels and because the wheel sits smaller in the arch, he had to cut it to a slight slope. The wheels are from a ’32 Ford and have been widened 2 inches towards the inside. The paint is inferno red from Chrysler’s Crossfire. All three of Francois’s cars are the same colour, but it definitely looks the best on the Delivery, the glint of which is much deeper. They were never able to replicate that same lustre again.
Because of the history behind the creativity of the Dodge mascot, Francois thought it very important to have the right one for his Dodge. The ram was made without having the original to look at. He searched extensively and eventually found one in the UK. Unfortunately with the import duty costs as well as what the guy wanted for it, it would have set Francois back a hefty 10K. He managed to procure pictures and dimensions of the mascot and had his artist friend recreate it out of clay.
The clay model was taken to another friend of his, a dental technician, who made an acrylic mould for it. This process eventually resulted in a bronze casting which he had chromed. He later found out that someone was selling a cut-off original and was based five minutes from where he lives. The front seats are from an old Ford 20M, and the back seats, are from a Datsun 1200 bakkie. Francois firmly believes that if your paint job and trim are not good then you cannot call the build a success.
Seeing that woodwork is Francois’s business, it was only natural that he would use his superior skills in creating the trim that adorns the interior. The dashboard is a fibreglass mould, the inside of which takes the shape of the car’s dash area. Its exterior “burl walnut veneer” has an interesting little side story to it. This veneer is from the base of the tree and is also the most expensive part. Except nobody knows what this particular veneer is.
It was used as packing material when it was sent from the UK. The supplier, where Francois gets his veneer kept it aside and said it was special. He then suggested that Francois find some use for it with regards to one of his cars. He did so and the end result is superb. To keep the vintage look, he concealed the sound system in the centre console which he also made. The wiring was done by his auto electrician friend Kallie. Further, the Dolphin gauges were purchased from Motown Autoparts in Cape Town. This build took about four years to complete. All three of Francois’s cars look astounding.